- Rimatex Dyechem
Rima print pigment emulsions can be best printed in combination with Rimaprint Binder on cotton, viscose, polyester, nylon fabrics and their blends. To obtain high degree of fastness properties on synthetic fabrics and blends the addition of fixer is recommended.
Rimaprint pigment emulsions and binders are based on oil in water emulsion system. The main
ingredients of Pigment printing past consists of :
Rimaprint Pigment Emulsion :
Rimaprint Pigment emulsion are based on selected pigment powedersand most efficient nonionic
emulsifiers thereby giving exceptionally fine particle size and good stability. Rimaprint
Pigment emulsions are easily miscible with each other in any proportion to produce desirable
with Rimaprint Binders.
-
Rimaprint Binders JLNThe most versatile Binders based on acrylic copolymer with high degree of resistance mechanical stress and various chemicals and imparts excellent fastness properties. Due to its excellent re-emulsification property. This Binder is Suitable for rotary screen printing besides roller. Screen and flat bed screen printing.
-
FixerThe addition of Fixer is recommended when printing is done on synthetic fabrics and their blends 1-2% of fixer can give good fastness properties. It is also recommended for khadi as well as Gold/Silver printing formulations.
-
Acid Liberating agents as catalystPhosphate being salt of weak acid is recommended to have good prints past stability as well as running property of the past.
-
Kerosene of mineral turpentine or synthetic thickenersUsually one has to add kerosene/mineral turpentine in Rimaprint Binder / water mixture containing, emulsifier under high speed stirrer to get stable emulsion. It can be possible to reduce or eliminate kerosene or mineral turpentine by using acrylic synthetic thickeners.
-
Reduction ThickeningThis is to obtain lower depth of shades from the standard print pastes. It is kept ready for conversion of standard print pastes into different strengths. Reduction thickening pastes is prepared in a similar manner as stock paste but using lower quantities of alkali (5%) and Rangolite (10%)
-
Preparation of the stock pastea) Preparation of 10% Binder stock reduction thickening10Parts Rimaprint Binder JLN05Parts Cepol LV 5% thickening02Parts Urea depending upon
the Atmospheric condition06Parts Water01Parts Emulsifier76Parts Kerosene or mineral turpentine
Under high speed stirringb) Preparation of stock paste using Incraprint IKF
(a synthetic thickener to substitute kerosene) Kerosene free system :4 - 4.5Parts Incraprint IKF85 - 84.5Parts Water10 – 10Parts Binder1 - 1Parts EmulsifierPreparation of print paste :
1-4Parts Rimaprint Pigment Emulsions4-4Parts Diammounium Phosphate(1:3) solution95-92Parts 10% Rimaprint Binder reduction thickening -
NotesDiammonium Phosphate is not to be added to Incraprint IKF stock paste Addition of extra binder is recommended above 4% shade to meet the ratio o0f pigment emulsion to binder to 1.2.5 The fabric printed with Rimaprint pigment emulsions / Binder system is fixed by curing at 140c for 5 minutes in hot air curing chamber Without guarantee
Rimatex Dyechem
Rima print pigment emulsions can be best printed in combination with Rimaprint Binder on cotton,
viscose, polyester, nylon fabrics and their blends. To obtain high degree of fastness properties on
synthetic fabrics and blends the addition of fixer is recommended.
Rimaprint pigment emulsions and binders are based on oil in water emulsion system. The main ingredients
of Pigment printing past consists of :
Rimaprint Pigment Emulsion :
Rimaprint Pigment emulsion are based on selected pigment powedersand most efficient nonionic emulsifiers thereby
giving exceptionally fine particle size and good stability. Rimaprint Pigment emulsions are easily miscible with
each other in any proportion to produce desirable with Rimaprint Binders.
Rimaprint Binders JLN :
The most versatile Binders based on acrylic copolymer with high degree of resistance mechanical stress
and various chemicals and imparts excellent fastness properties. Due to its excellent re-emulsification property.
This Binder is Suitable for rotary screen printing besides roller. Screen and flat bed screen printing.
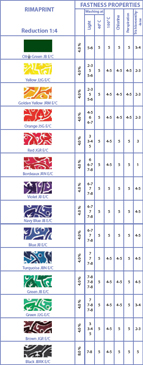
Preparation of the stock paste :
a) Preparation of 10% Binder stock reduction thickening10
Parts
Rimaprint Binder JLN
05
Parts
Cepol LV 5% thickening
02
Parts
Urea depending upon
the Atmospheric condition
the Atmospheric condition
06
Parts
Water
01
Parts
Emulsifier
76
Parts
Kerosene or mineral turpentine
Under high speed stirring
Under high speed stirring
b) Preparation of stock paste using Incraprint IKF
(a synthetic thickener to substitute kerosene) Kerosene free system :
4 - 4.5
Parts
Incraprint IKF
85 - 84.5
Parts
Water
10 – 10
Parts
Binder
1 - 1
Parts
Emulsifier
Preparation of print paste :
1-4
Parts
Rimaprint Pigment Emulsions
4-4
Parts
Diammounium Phosphate(1:3) solution
95-92
Parts
10% Rimaprint Binder reduction thickening
Diammonium Phosphate is not to be added to Incraprint IKF stock paste Addition of extra binder is recommended above 4% shade to meet the ratio o0f pigment emulsion to binder to 1.2.5 The fabric printed with Rimaprint pigment emulsions / Binder system is fixed by curing at 140c for 5 minutes in hot air curing chamber
Without guarantee